La gestion de la maintenance dans le secteur industriel est souvent complexe et chronophage. Mais saviez-vous qu’une solution de gestion de maintenance assistée par ordinateur (GMAO) peut transformer cette tâche en un processus fluide et efficace ? Si vous vous demandez pourquoi une GMAO est indispensable pour vos projets de maintenance, ou comment elle peut optimiser vos opérations, vous êtes au bon endroit.
Dans cet article, nous allons explorer en détail les raisons pour lesquelles une GMAO est essentielle pour la gestion de vos projets de maintenance, ainsi que les étapes clés pour planifier, suivre et analyser l’avancement de vos projets. Vous découvrirez également les indicateurs de performance à surveiller et les meilleures pratiques à adopter pour optimiser vos processus de maintenance.
Prêt à révolutionner votre gestion de maintenance ? Plongeons ensemble dans l’univers des solutions GMAO et découvrez comment elles peuvent répondre à vos besoins spécifiques.
Pourquoi une GMAO est essentielle pour la gestion de projets de maintenance ?
Dans le secteur industriel, la gestion des projets de maintenance est une tâche complexe qui nécessite une organisation rigoureuse et une coordination parfaite entre les différents intervenants. L’utilisation d’un système de gestion de maintenance assistée par ordinateur (GMAO) s’avère être une solution incontournable pour optimiser cette gestion. Mais pourquoi est-elle si cruciale ?
Amélioration des performances opérationnelles
Une GMAO permet d’améliorer significativement les performances opérationnelles de votre entreprise. En centralisant toutes les informations relatives à la maintenance de vos équipements, elle facilite l’accès aux données cruciales et permet une prise de décision rapide et éclairée. Par exemple, dans une usine de production de ciment, le suivi en temps réel des interventions de maintenance permet de réduire les temps d’arrêt machine et d’optimiser les cycles de production.
Gestion optimisée des équipements
Le recours à un logiciel de gestion de maintenance vous permet d’assurer une gestion optimale de vos équipements. En automatisant la planification des interventions et en suivant l’historique des maintenances, vous pouvez anticiper les pannes et prolonger la durée de vie de vos machines. Prenons l’exemple d’une industrie pétrochimique : la GMAO permet de suivre les cycles de maintenance préventive des pompes et compresseurs, évitant ainsi des pannes coûteuses et des interruptions de production.
Réduction des coûts
Un autre avantage majeur d’un système logiciel de maintenance est la réduction des coûts. En optimisant les processus de maintenance et en limitant les interventions d’urgence, vous pouvez réaliser des économies substantielles. Dans le secteur de la métallurgie, par exemple, une GMAO permet de réduire les coûts liés aux pièces de rechange et à la main-d’œuvre en planifiant efficacement les interventions et en gérant les stocks de manière proactive.
Conformité et traçabilité
Enfin, une GMAO assure la conformité aux normes industrielles et réglementaires. En documentant toutes les interventions et en conservant un historique détaillé, elle garantit une traçabilité complète des opérations de maintenance. Dans l’industrie pharmaceutique, par exemple, le respect des normes de qualité et de sécurité est essentiel, et un système de gestion de maintenance permet de répondre à ces exigences avec précision.
En résumé, l’utilisation d’un outil de gestion de maintenance assistée par ordinateur est indispensable pour toute entreprise industrielle souhaitant optimiser la gestion de ses projets de maintenance. Elle apporte une amélioration notable des performances opérationnelles, une gestion optimisée des équipements, une réduction des coûts et une conformité accrue aux normes en vigueur.
Les étapes clés pour planifier vos projets de maintenance avec une GMAO
Définir les objectifs de maintenance
Pour une planification réussie, il est crucial de commencer par définir des objectifs clairs. Ces objectifs peuvent inclure la réduction des temps d’arrêt, l’amélioration de la durée de vie des équipements, ou encore l’optimisation des coûts de maintenance. Un système logiciel de gestion vous permet de centraliser ces objectifs et de les aligner avec les besoins opérationnels de votre industrie.
Établir un calendrier de maintenance
La planification des interventions de maintenance doit être rigoureuse. Grâce à un outil de gestion, vous pouvez créer un calendrier de maintenance précis, intégrant les interventions préventives et correctives. Ce calendrier prend en compte les disponibilités des équipements et des techniciens, ce qui permet de minimiser les interruptions de production. Par exemple, une usine de fabrication de produits chimiques peut planifier les maintenances pendant les périodes de faible activité pour éviter les pertes de production.
Allouer les ressources nécessaires
Une fois le calendrier établi, il est essentiel de déterminer les ressources nécessaires pour chaque tâche de maintenance. Un système de maintenance vous aide à allouer efficacement les techniciens, les pièces détachées et les outils requis. Cela permet non seulement de réduire les temps d’intervention, mais aussi de s’assurer que chaque tâche est réalisée dans les meilleures conditions possibles. Par exemple, dans une aciérie, la disponibilité des pièces de rechange critiques peut être suivie en temps réel pour éviter les retards.
Évaluer les risques et établir des priorités
La gestion des risques est une composante essentielle de la planification de projets de maintenance. Un logiciel de gestion de maintenance vous permet d’identifier les équipements critiques et d’évaluer les risques associés à leur défaillance. En conséquence, vous pouvez établir des priorités pour les interventions, en vous concentrant sur les équipements dont la défaillance aurait le plus grand impact sur la production. Par exemple, dans une raffinerie de pétrole, les unités de distillation peuvent être classées comme prioritaires en raison de leur rôle central dans le processus de production.
Suivi et mise à jour en temps réel
La planification initiale doit être suivie et mise à jour en continu. Un système de gestion de maintenance offre des fonctionnalités de suivi en temps réel, permettant d’ajuster les plans en fonction des nouvelles données et des imprévus. Par exemple, si une panne imprévue se produit dans une ligne de production automobile, le plan de maintenance peut être ajusté immédiatement pour minimiser l’impact sur la production.
En suivant ces étapes clés, vous pouvez maximiser l’efficacité de vos projets de maintenance et assurer une gestion optimale de vos équipements industriels.
Comment suivre efficacement l’avancement de vos projets de maintenance grâce à une GMAO
Dans le cadre de l’industrie, suivre l’avancement des projets de maintenance est une tâche cruciale pour garantir la disponibilité et la performance des équipements. Un système de gestion de maintenance assistée par ordinateur (GMAO) offre des outils puissants pour superviser ces projets de manière efficace.
Des tableaux de bord personnalisés pour une vision d’ensemble
Un des principaux atouts d’un logiciel de gestion de maintenance est la possibilité de configurer des tableaux de bord personnalisés. Ces tableaux de bord offrent une vision globale de l’état de vos projets de maintenance, en affichant des indicateurs clés tels que le taux d’avancement, les tâches en cours, et les ressources allouées. Par exemple, dans une usine de production de métaux, un tableau de bord peut montrer le statut des interventions de maintenance préventive sur les fours de fusion, permettant aux responsables de réagir rapidement en cas de retard.
Suivi en temps réel des interventions
Grâce à un outil de maintenance, vous pouvez suivre en temps réel les interventions sur vos équipements. Cela inclut la réception des notifications instantanées lorsque des tâches sont commencées ou terminées. Pour une raffinerie pétrolière, par exemple, le suivi en temps réel permet de s’assurer que les opérations de maintenance sur les pipelines sont exécutées selon le planning, réduisant ainsi les risques de fuites ou d’incidents.
Gestion des ressources et des compétences
Un système logiciel de gestion de maintenance permet également de gérer efficacement les ressources humaines et matérielles. En attribuant les bonnes compétences aux tâches appropriées, vous optimisez l’utilisation de votre personnel. Dans le secteur de la production chimique, cela signifie que vous pouvez assigner des techniciens spécialisés aux interventions sur des équipements critiques, garantissant ainsi une maintenance de haute qualité et minimisant les temps d’arrêt.
Rapports détaillés et historiques
Enfin, un logiciel de gestion de maintenance génère des rapports détaillés sur chaque projet de maintenance, incluant l’historique des interventions, les consommables utilisés, et les temps de travail. Ces rapports sont essentiels pour analyser les performances et identifier les axes d’amélioration. Par exemple, dans une centrale électrique, les rapports peuvent révéler des tendances de pannes récurrentes sur certains équipements, permettant de planifier des actions correctives plus ciblées.
En intégrant ces fonctionnalités, un système de gestion de maintenance optimise non seulement le suivi des projets, mais améliore également la performance opérationnelle de vos installations industrielles.
Analyser les performances de vos projets de maintenance : les indicateurs à surveiller avec une GMAO
Pour garantir l’efficacité de vos projets de maintenance, il est crucial de surveiller certains indicateurs de performance clés (KPI). Un système de gestion de maintenance assistée par ordinateur vous permet de suivre ces indicateurs de manière rigoureuse et précise. Voici les principaux KPI à surveiller pour optimiser la gestion de vos projets de maintenance.
Temps moyen entre pannes (MTBF)
Le temps moyen entre pannes (MTBF) est un indicateur essentiel pour évaluer la fiabilité de vos équipements. En surveillant le MTBF à l’aide de votre solution logicielle, vous pouvez identifier les équipements qui nécessitent des interventions fréquentes et planifier des actions correctives pour améliorer leur performance. Par exemple, dans une usine de production de ciment, suivre le MTBF des broyeurs permet de réduire les arrêts imprévus et d’optimiser le processus de production.
Temps moyen de réparation (MTTR)
Le temps moyen de réparation (MTTR) mesure la rapidité avec laquelle vos équipes de maintenance peuvent réparer un équipement en panne. Un outil de gestion de maintenance vous aide à analyser le MTTR et à identifier les goulots d’étranglement dans le processus de réparation. En réduisant le MTTR, vous améliorez la disponibilité de vos équipements et minimisez les interruptions de production. Par exemple, dans une aciérie, réduire le MTTR des fours de fusion permet de maintenir une production continue et d’augmenter la rentabilité.
Taux de disponibilité des équipements
Le taux de disponibilité des équipements est un indicateur crucial pour évaluer l’efficacité de votre système de maintenance. Un logiciel de gestion de maintenance vous permet de suivre ce taux en temps réel et d’identifier les équipements qui posent des problèmes de fiabilité. En améliorant la disponibilité de vos équipements, vous pouvez maximiser la productivité et réduire les coûts de maintenance. Par exemple, dans une raffinerie de pétrole, améliorer la disponibilité des pompes et des compresseurs permet d’assurer un flux de production ininterrompu et d’éviter les pertes financières.
Coût de maintenance par équipement
Le coût de maintenance par équipement est un indicateur essentiel pour gérer votre budget de maintenance de manière efficace. Un système de gestion vous permet de suivre les coûts associés à chaque équipement et d’identifier les postes de dépenses les plus importants. En optimisant les coûts de maintenance, vous pouvez allouer vos ressources de manière plus stratégique et améliorer la rentabilité de vos opérations. Par exemple, dans une usine de fabrication de papier, réduire les coûts de maintenance des machines de découpe permet de diminuer les dépenses opérationnelles et d’augmenter la marge bénéficiaire.
En surveillant ces indicateurs de performance avec un outil de maintenance performant, vous pouvez non seulement améliorer la fiabilité et la disponibilité de vos équipements, mais aussi optimiser vos processus de maintenance et réduire les coûts associés. Une gestion rigoureuse et proactive de vos projets de maintenance est essentielle pour garantir le succès de vos opérations industrielles.
Optimiser vos processus de maintenance : les meilleures pratiques à adopter avec une GMAO
L’optimisation des processus de maintenance est un enjeu crucial pour toute industrie cherchant à améliorer ses performances opérationnelles. L’utilisation d’un outil de gestion de maintenance permet de structurer et d’améliorer ces processus de manière significative. Voici quelques meilleures pratiques à adopter pour tirer le meilleur parti de votre système logiciel de maintenance.
Centraliser les informations
L’une des premières étapes pour optimiser vos processus de maintenance est de centraliser toutes les informations relatives à vos équipements et interventions. Un système de gestion de maintenance permet de collecter, stocker et organiser ces données de manière cohérente. Cela inclut les historiques de maintenance, les manuels techniques, les contrats de service, et bien plus encore. En ayant toutes ces informations accessibles en un seul endroit, vous pouvez réduire les temps de recherche et améliorer la prise de décision.
Automatiser les tâches récurrentes
L’automatisation des tâches récurrentes est une autre pratique essentielle. Utilisez votre solution logicielle pour automatiser la planification des interventions préventives, les notifications de maintenance, et même l’approvisionnement des pièces de rechange. Cela permet non seulement de réduire les erreurs humaines, mais également de libérer du temps pour vos équipes, leur permettant de se concentrer sur des tâches à plus forte valeur ajoutée.
Analyser les données pour une maintenance prédictive
Les systèmes de gestion de maintenance modernes intègrent souvent des capacités d’analyse avancées. Utilisez ces fonctionnalités pour analyser les données collectées et identifier des tendances ou des anomalies. Cette approche analytique permet de passer d’une maintenance réactive à une maintenance prédictive, anticipant ainsi les pannes avant qu’elles ne surviennent et minimisant les temps d’arrêt imprévus.
Former vos équipes
Pour maximiser l’efficacité de votre outil de maintenance, il est crucial de former vos équipes à son utilisation. Assurez-vous que tous les utilisateurs, des techniciens aux gestionnaires, comprennent comment utiliser les différentes fonctionnalités du système logiciel. Une formation adéquate garantit une adoption réussie et une utilisation optimale de l’outil.
Suivre et améliorer continuellement
Enfin, l’optimisation des processus de maintenance est un effort continu. Utilisez les indicateurs de performance fournis par votre système de gestion pour évaluer régulièrement l’efficacité de vos processus de maintenance. Identifiez les domaines nécessitant des améliorations et apportez les ajustements nécessaires pour maintenir un haut niveau de performance.
En adoptant ces meilleures pratiques, vous pouvez transformer votre gestion de maintenance en un processus fluide et efficace, réduisant les coûts et améliorant la fiabilité de vos équipements.
Conclusion : adoptez une GMAO pour optimiser vos projets de maintenance
En conclusion, l’intégration d’un système de gestion de maintenance assistée par ordinateur est une étape incontournable pour toute entreprise industrielle souhaitant optimiser ses projets de maintenance. Grâce à une GMAO, vous pouvez non seulement améliorer vos performances opérationnelles, mais aussi assurer une gestion optimale de vos équipements, réduire vos coûts et garantir la conformité aux normes en vigueur.
En adoptant les meilleures pratiques décrites dans cet article, vous pouvez transformer votre gestion de maintenance en un processus fluide et efficace. Centralisez vos informations, automatisez les tâches récurrentes, analysez les données pour une maintenance prédictive, formez vos équipes et suivez continuellement les indicateurs de performance pour des améliorations constantes.
Ne laissez pas les défis de la maintenance freiner la performance de vos opérations industrielles. Investissez dans une GMAO et prenez le contrôle de vos projets de maintenance pour garantir la fiabilité et la disponibilité de vos équipements. Optimisez dès maintenant vos processus et assurez-vous que votre gestion de maintenance est à la hauteur des exigences de votre secteur.
FAQ sur l’importance d’une GMAO pour la gestion de projets de maintenance
1. Quels sont les principaux avantages d’utiliser une GMAO pour la gestion de projets de maintenance ?
Une solution de gestion de maintenance offre plusieurs avantages clés :
- Amélioration des performances opérationnelles : En centralisant toutes les données de maintenance, elle permet une prise de décision rapide et éclairée.
- Gestion optimisée des équipements : En automatisant la planification et en suivant l’historique des interventions, elle anticipe les pannes et prolonge la durée de vie des machines.
- Réduction des coûts : Elle minimise les interventions d’urgence et optimise la gestion des stocks, ce qui réduit les coûts de maintenance.
- Conformité et traçabilité : Elle garantit la conformité aux normes industrielles en documentant toutes les interventions et en conservant un historique détaillé.
2. Comment une GMAO peut-elle améliorer la gestion des équipements dans l’industrie ?
Une solution logicielle de gestion de maintenance permet d’automatiser la planification des interventions et de suivre l’historique des maintenances. Cela permet d’anticiper les pannes et de prolonger la durée de vie des équipements. Par exemple, dans une industrie pétrochimique, la GMAO peut suivre les cycles de maintenance préventive des pompes et compresseurs, évitant ainsi des pannes coûteuses et des interruptions de production.
3. Quels indicateurs de performance surveiller avec une GMAO pour optimiser la maintenance ?
Les principaux indicateurs de performance à surveiller avec une solution de gestion de maintenance incluent :
- Temps moyen entre pannes (MTBF) : Mesure la fiabilité des équipements.
- Temps moyen de réparation (MTTR) : Évalue la rapidité des interventions de maintenance.
- Taux de disponibilité des équipements : Indique l’efficacité de la maintenance.
- Coût de maintenance par équipement : Aide à gérer le budget de maintenance de manière efficace.
4. Quelles sont les meilleures pratiques pour optimiser les processus de maintenance avec une GMAO ?
Pour optimiser les processus de maintenance avec une solution logicielle de maintenance, il est recommandé de :
- Centraliser les informations : Collecter, stocker et organiser toutes les données de maintenance en un seul endroit.
- Automatiser les tâches récurrentes : Planifier les interventions préventives et gérer les notifications et l’approvisionnement des pièces de rechange automatiquement.
- Analyser les données : Utiliser les capacités analytiques pour identifier les tendances et passer à une maintenance prédictive.
- Former les équipes : Assurer une formation adéquate pour une utilisation optimale de l’outil de gestion.
- Suivre et améliorer continuellement : Utiliser les KPI pour évaluer et ajuster les processus de maintenance régulièrement.
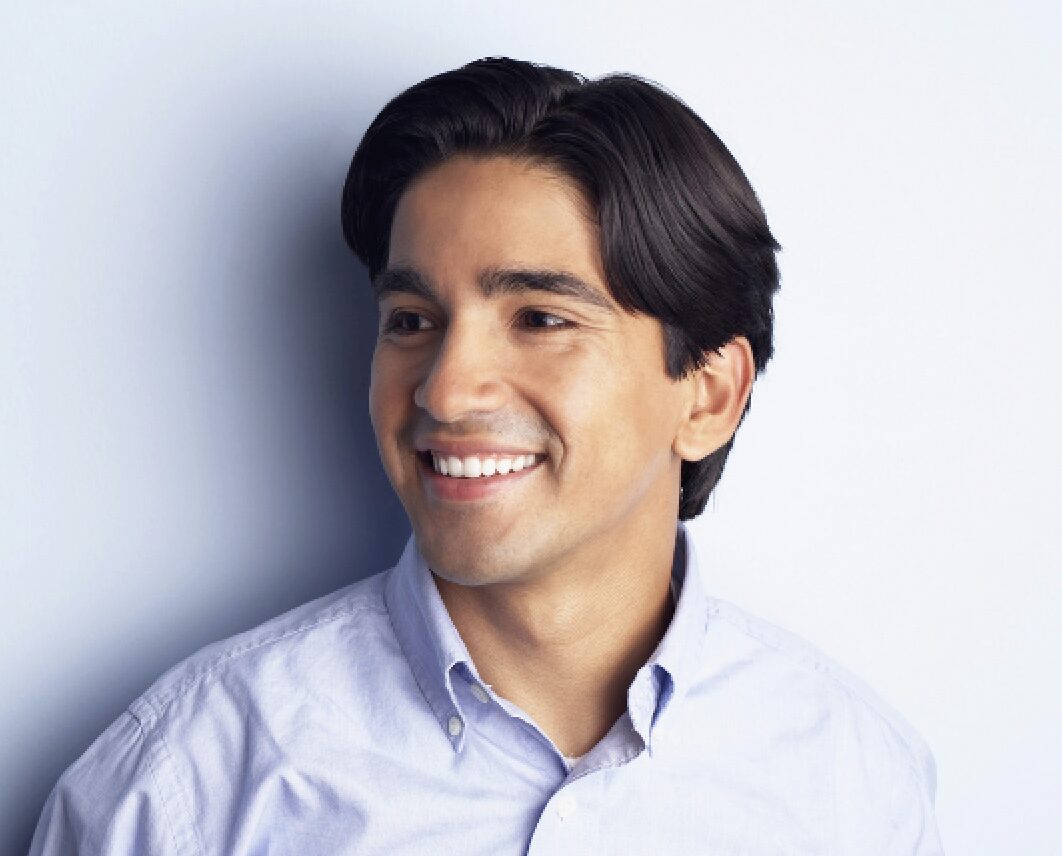
Consultant chez Solvay, j’accompagne les entreprises dans l’optimisation de leurs stratégies de maintenance, en mettant à profit mon expertise en GMAO et gestion des actifs industriels. Je partage également des conseils pratiques et études de cas sur gmao-industrie.fr, afin d’aider les entreprises à améliorer leurs performances opérationnelles.
0 commentaires