La gestion des incidents dans le secteur industriel est un défi constant. Les entreprises cherchent sans cesse des moyens d’optimiser leurs processus et de réduire les temps d’arrêt. Avez-vous déjà réfléchi à l’impact que pourrait avoir une gestion centralisée des incidents sur votre productivité? Dans cet article, nous allons explorer les nombreux bénéfices qu’une solution de gestion de maintenance assistée par ordinateur (GMAO) peut apporter à vos opérations. De l’optimisation des processus à la gestion proactive des incidents, découvrez comment une GMAO peut transformer votre approche de la maintenance.
Optimisation des processus : comment une GMAO révolutionne la gestion des incidents
Dans le secteur industriel, la gestion des incidents est un élément crucial pour assurer la continuité des opérations. L’intégration d’une solution de gestion de maintenance assistée par ordinateur (GMAO) permet de centraliser et d’optimiser cette gestion de manière significative. En centralisant les informations relatives aux incidents, un système logiciel permet de rationaliser les processus de maintenance et de réduire les inefficacités.
Par exemple, un outil de gestion permet de consigner chaque incident dès qu’il se produit, offrant ainsi une visibilité immédiate et complète sur l’état de vos équipements. Les techniciens peuvent accéder rapidement aux informations nécessaires, ce qui permet un diagnostic plus rapide et une résolution plus efficace des problèmes. De plus, la centralisation des données dans un système unique évite les duplications et les erreurs liées à la saisie manuelle.
Grâce à l’automatisation des tâches répétitives et à la planification optimisée des interventions, une solution logicielle permet de libérer du temps pour les équipes de maintenance, leur permettant de se concentrer sur des tâches à plus forte valeur ajoutée. Par conséquent, l’optimisation des processus de gestion des incidents par un système de maintenance se traduit par une amélioration significative des performances opérationnelles.
En outre, l’utilisation d’un logiciel de gestion de maintenance permet de mettre en place des workflows standardisés, garantissant que chaque incident est traité de manière cohérente et conforme aux procédures internes. Cela contribue non seulement à améliorer l’efficacité, mais aussi à renforcer la sécurité et la conformité aux réglementations en vigueur.
Réduction des temps d’arrêt : l’impact direct d’une GMAO sur la productivité
Dans le secteur industriel, les arrêts non planifiés peuvent coûter des milliers, voire des millions d’euros. Une solution logicielle de gestion de maintenance joue un rôle crucial en réduisant ces temps d’arrêt grâce à une gestion centralisée des incidents. Par exemple, lorsque vos équipements critiques tombent en panne, une GMAO permet de déclencher des alertes immédiates aux équipes de maintenance, garantissant une intervention rapide.
En centralisant les données, le système de gestion permet de prioriser les interventions en fonction de la criticité des incidents. Ainsi, les pannes majeures sont traitées en priorité, minimisant les interruptions de production. De plus, grâce à un historique détaillé des incidents, les techniciens peuvent identifier rapidement les causes récurrentes et mettre en place des actions correctives efficaces.
Un exemple concret d’application se trouve dans l’industrie lourde, où la disponibilité des équipements est essentielle pour le maintien des chaînes de production. Grâce à un outil de gestion, les entreprises peuvent surveiller en temps réel l’état de leurs machines et planifier des maintenances préventives. Cela permet non seulement de réduire les pannes mais aussi d’optimiser l’utilisation des ressources, en évitant les interventions superflues.
En résumé, l’utilisation d’un système logiciel de gestion des incidents contribue directement à améliorer la productivité en réduisant les temps d’arrêt. Il permet une meilleure planification, une réactivité accrue et une gestion efficace des ressources, assurant ainsi une disponibilité maximale des équipements.
Amélioration de la traçabilité : suivi précis et historique des incidents
La traçabilité des incidents est un enjeu majeur pour toute entreprise industrielle cherchant à optimiser sa gestion de maintenance. Grâce à une solution logicielle de gestion de maintenance, vous pouvez bénéficier d’un suivi détaillé et d’un historique exhaustif des incidents. En centralisant toutes les informations relatives aux pannes et aux interventions, ces systèmes permettent une vision claire et globale de la situation.
Suivi en temps réel
Un des avantages immédiats d’un système de maintenance est la capacité de suivre les incidents en temps réel. Chaque événement est enregistré dès qu’il survient, permettant aux équipes de maintenance d’intervenir rapidement et efficacement. Par exemple, dans une usine de production de pièces automobiles, la moindre défaillance sur une chaîne de montage peut entraîner des retards coûteux. Avec un outil de gestion, les techniciens sont immédiatement alertés et peuvent consulter l’historique des interventions pour identifier des solutions éprouvées.
Historique complet des interventions
Un autre bénéfice clé est la possibilité de consulter l’historique des incidents et des interventions. Cela permet non seulement d’identifier des tendances récurrentes, mais aussi de prendre des décisions éclairées pour l’amélioration continue des processus de maintenance. Par exemple, dans une centrale électrique, avoir accès à l’historique détaillé des pannes de turbines peut aider à anticiper et à prévenir les incidents futurs, réduisant ainsi les temps d’arrêt imprévus.
Prise de décisions éclairées
Enfin, la traçabilité accrue offerte par une solution logicielle facilite la prise de décisions stratégiques. En disposant de données précises et actualisées, les managers peuvent élaborer des plans de maintenance préventive plus efficaces et optimiser les ressources. Par exemple, une entreprise de production chimique peut utiliser les données collectées pour réajuster les calendriers d’entretien des réacteurs, améliorant ainsi la fiabilité des équipements et la sécurité des opérations.
Gestion proactive : anticiper les incidents grâce à une GMAO performante
L’une des forces majeures d’un système de gestion de maintenance assistée par ordinateur réside dans sa capacité à anticiper les incidents avant qu’ils ne surviennent. En effet, une solution logicielle performante permet de mettre en place une gestion proactive, qui se traduit par une réduction significative des interruptions imprévues et une amélioration continue des performances opérationnelles.
Surveillance continue des équipements
Grâce à une surveillance continue des équipements, le système de maintenance peut détecter les signes avant-coureurs de défaillances potentielles. Par exemple, dans une industrie lourde telle que la métallurgie, le logiciel de gestion de maintenance peut surveiller les vibrations des machines, les températures ou encore les niveaux de lubrification. Ces données sont ensuite analysées pour identifier les anomalies et alerter les équipes de maintenance avant que des pannes ne surviennent. Cette approche permet non seulement de prévenir les incidents, mais aussi d’optimiser les interventions de maintenance.
Planification et priorisation des interventions
Un autre avantage clé de la gestion proactive est la capacité à planifier et à prioriser les interventions de manière efficace. En utilisant les données collectées et analysées par le système, les responsables de maintenance peuvent établir des calendriers d’entretien préventif et prioriser les tâches en fonction de la criticité des équipements. Par exemple, dans une usine de production chimique, les équipements critiques pour la sécurité et la production peuvent être entretenus plus fréquemment, tandis que les équipements moins critiques peuvent être planifiés pour des interventions à des intervalles plus longs, mais toujours avant qu’un incident ne survienne.
Amélioration continue et retour d’expérience
En outre, une solution logicielle de gestion de maintenance permet de tirer des leçons des incidents passés et d’améliorer continuellement les processus de maintenance. Chaque intervention et chaque incident sont documentés, ce qui constitue une base de données précieuse pour analyser les tendances et identifier les points faibles des équipements. Par exemple, dans une raffinerie de pétrole, les analyses post-intervention peuvent révéler des schémas récurrents de défaillances sur certaines pompes ou compresseurs, permettant ainsi de mettre en place des actions correctives ciblées et d’améliorer la fiabilité globale des installations.
En intégrant ces fonctionnalités, une GMAO performante transforme la gestion des incidents en une approche proactive, permettant ainsi aux industries de maximiser la disponibilité de leurs équipements et de réduire les coûts associés aux pannes imprévues.
Analyse des données : exploitez les rapports et indicateurs pour une gestion optimale
L’un des avantages majeurs de l’utilisation d’un système logiciel dans la gestion des incidents est la capacité à exploiter de manière efficace et détaillée les données recueillies. En effet, les outils de gestion de maintenance modernes offrent des fonctionnalités avancées d’analyse des données, permettant aux entreprises industrielles d’optimiser leurs performances opérationnelles.
Rapports personnalisés pour une vision claire
Grâce aux solutions logicielles de gestion de maintenance, il est possible de générer des rapports personnalisés en fonction des besoins spécifiques de votre activité. Ces rapports fournissent une vue d’ensemble précise des incidents survenus, des temps de réponse et des actions correctives mises en place. Par exemple, un responsable de maintenance peut facilement visualiser les tendances récurrentes et identifier les équipements nécessitant une attention particulière. Cela permet de prendre des décisions éclairées et d’allouer les ressources de manière plus efficiente.
Indicateurs de performance pour un suivi rigoureux
Les indicateurs clés de performance (KPI) sont essentiels pour mesurer l’efficacité de votre gestion des incidents. Un outil de gestion performant offre une multitude de KPI, tels que le temps moyen de réparation (MTTR), le temps moyen entre pannes (MTBF) et le taux de disponibilité des équipements. En surveillant ces indicateurs, vous pouvez détecter rapidement les anomalies et ajuster vos stratégies de maintenance en conséquence. Par exemple, une diminution du MTTR peut indiquer une amélioration de la réactivité de votre équipe de maintenance, tandis qu’une augmentation du MTBF peut signaler une meilleure fiabilité de vos équipements.
Prédiction et prévention grâce à l’analyse des données
L’analyse des données ne se limite pas à la simple visualisation de rapports et d’indicateurs. Les systèmes de maintenance avancés intègrent également des outils de prédiction basés sur l’intelligence artificielle et le machine learning. Ces technologies permettent d’anticiper les pannes potentielles et de planifier les interventions de manière proactive. Par exemple, en analysant les données historiques et les conditions de fonctionnement des équipements, le logiciel peut prévoir les défaillances imminentes et recommander des actions préventives. Cela se traduit par une réduction significative des temps d’arrêt non planifiés et une amélioration de la disponibilité des machines.
Exemples concrets d’utilisation dans l’industrie lourde
Dans les secteurs industriels tels que la sidérurgie, la pétrochimie ou encore l’aéronautique, l’utilisation d’un système de gestion de maintenance assistée par ordinateur est cruciale. Prenons l’exemple d’une usine de production de ciment. En utilisant un logiciel de gestion de maintenance, l’équipe peut suivre en temps réel les performances des broyeurs et des fours. Les rapports détaillés permettent d’identifier rapidement les incidents récurrents et de mettre en place des actions correctives ciblées. De plus, les indicateurs de performance aident à optimiser les cycles de maintenance préventive, évitant ainsi les arrêts imprévus et améliorant la productivité globale de l’usine.
En conclusion, l’intégration d’un système logiciel de gestion de maintenance dans votre entreprise industrielle permet d’exploiter pleinement les données disponibles pour améliorer la gestion des incidents. Les rapports personnalisés, les indicateurs de performance et les outils de prédiction offrent une vision claire et précise de vos opérations, vous permettant d’optimiser vos processus de maintenance et d’accroître la performance de vos équipements.
En conclusion, adopter une solution de gestion de maintenance assistée par ordinateur (GMAO) est un levier puissant pour optimiser la gestion des incidents dans votre industrie. En centralisant les données, en automatisant les tâches répétitives et en offrant une traçabilité exhaustive, une GMAO performante transforme la manière dont vos équipes de maintenance opèrent. Ce système permet non seulement de réduire les temps d’arrêt et d’améliorer la disponibilité des équipements, mais aussi d’anticiper et de prévenir les pannes potentielles grâce à une gestion proactive. En exploitant les rapports personnalisés et les indicateurs de performance, vous pouvez prendre des décisions éclairées et ajuster vos stratégies de maintenance pour maximiser l’efficacité opérationnelle. Ne laissez plus les incidents imprévus freiner vos opérations : intégrez une GMAO dans votre processus de maintenance et profitez des nombreux avantages qu’elle offre.
FAQ sur la GMAO et la gestion des incidents
1. Comment une GMAO peut-elle améliorer la réactivité de vos équipes de maintenance en cas d’incident ?
Une solution de gestion de maintenance assistée par ordinateur (GMAO) centralise toutes les informations relatives aux incidents et aux équipements. Dès qu’un incident survient, le système déclenche des alertes automatiques aux équipes de maintenance, leur permettant d’intervenir rapidement. En accédant à des données complètes et mises à jour en temps réel, les techniciens peuvent diagnostiquer et résoudre les problèmes plus efficacement, réduisant ainsi les temps d’arrêt et améliorant la continuité des opérations.
2. Quels sont les avantages d’une GMAO pour la planification des interventions de maintenance ?
Une GMAO permet de mettre en place des workflows standardisés et de planifier les interventions de manière optimale. En analysant les données historiques et les tendances des incidents, le système peut prioriser les tâches en fonction de la criticité des équipements. Cela garantit que les pannes majeures sont traitées en priorité et que les maintenances préventives sont planifiées de manière à minimiser les interruptions de production. Par exemple, dans une usine de production chimique, les équipements critiques peuvent être entretenus plus fréquemment pour prévenir les incidents et assurer une production continue.
3. Comment une GMAO contribue-t-elle à la traçabilité et à l’historique des incidents ?
Une solution logicielle de gestion de maintenance consigne chaque incident et chaque intervention dans un historique détaillé. Cela permet aux entreprises de suivre précisément les pannes et les réparations effectuées, offrant une vision claire et globale de la situation des équipements. En consultant cet historique, les techniciens peuvent identifier des tendances récurrentes et mettre en place des actions correctives ciblées. Par exemple, dans une centrale électrique, l’historique des pannes de turbines peut aider à anticiper les défaillances futures et à améliorer la fiabilité des équipements.
4. En quoi l’analyse des données d’une GMAO peut-elle optimiser la gestion des incidents ?
Les systèmes de gestion de maintenance avancés offrent des fonctionnalités d’analyse des données, permettant de générer des rapports personnalisés et de suivre des indicateurs de performance clés (KPI). Ces outils permettent de visualiser les tendances des incidents, d’identifier les équipements nécessitant une attention particulière et de prendre des décisions éclairées pour optimiser les processus de maintenance. Par exemple, en utilisant des outils de prédiction basés sur l’intelligence artificielle, une entreprise de production peut anticiper les pannes potentielles et planifier des interventions préventives, réduisant ainsi les temps d’arrêt non planifiés et améliorant la disponibilité des machines.
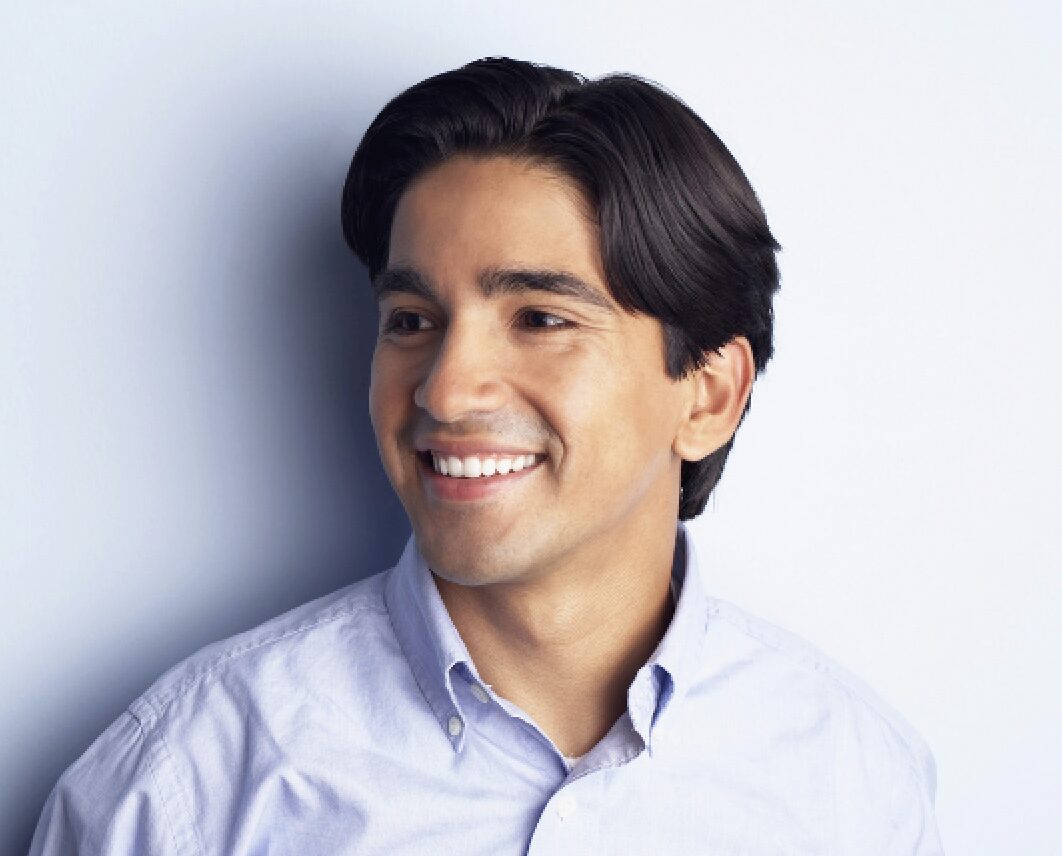
Consultant chez Solvay, j’accompagne les entreprises dans l’optimisation de leurs stratégies de maintenance, en mettant à profit mon expertise en GMAO et gestion des actifs industriels. Je partage également des conseils pratiques et études de cas sur gmao-industrie.fr, afin d’aider les entreprises à améliorer leurs performances opérationnelles.
0 commentaires