Dans un secteur industriel en constante évolution, la gestion efficace de la maintenance des équipements est cruciale pour maintenir la compétitivité et garantir une production sans faille. Mais comment les entreprises peuvent-elles optimiser cette gestion tout en réduisant les coûts et en améliorant la productivité ? La réponse réside dans l’adoption d’une GMAO. Cet article explore les raisons fondamentales pour lesquelles une GMAO peut transformer vos opérations, de l’optimisation des coûts à l’amélioration de la disponibilité des équipements. Vous découvrirez également comment une gestion proactive et préventive peut prolonger la durée de vie de vos machines tout en assurant leur conformité et leur sécurité. Prêt à découvrir comment maximiser l’efficacité de votre maintenance industrielle ? Lisez la suite pour tout savoir sur les avantages d’une GMAO pour vos équipements industriels.
Pourquoi adopter une GMAO pour la maintenance des équipements industriels ?
Dans le secteur industriel, la maintenance des équipements est une composante essentielle pour assurer la continuité des opérations et la performance globale. Adopter une solution logicielle de gestion de maintenance assistée par ordinateur (GMAO) présente de nombreux avantages pour les entreprises industrielles. Voici quelques raisons fondamentales pour lesquelles vous devriez envisager cette solution.
Optimisation des coûts de maintenance grâce à la GMAO équipements industriels
L’un des avantages les plus tangibles de l’adoption d’un système de gestion de maintenance assistée par ordinateur réside dans l’optimisation des coûts de maintenance. En intégrant un outil de gestion performant, les entreprises industrielles peuvent réaliser des économies significatives tout en améliorant l’efficacité de leurs opérations.
Réduction des coûts de maintenance corrective
La maintenance corrective, souvent imprévisible et coûteuse, peut être considérablement réduite grâce à un logiciel de gestion de maintenance. En surveillant en temps réel l’état de vos équipements, le système logiciel permet de détecter les anomalies avant qu’elles ne se transforment en pannes majeures. Cette approche proactive évite des interventions d’urgence coûteuses et minimise les temps d’arrêt non planifiés, ce qui se traduit par une meilleure maîtrise des budgets de maintenance.
Optimisation des ressources et des interventions
Un outil de maintenance efficace permet également d’optimiser l’utilisation des ressources, tant humaines que matérielles. Grâce à une planification rigoureuse des interventions, vous pouvez allouer les bonnes compétences au bon moment, évitant ainsi les surcharges de travail ou les périodes d’inactivité. De plus, le système de gestion permet de suivre l’inventaire des pièces de rechange, assurant ainsi une disponibilité optimale sans surstockage coûteux.
Prolongation de la durée de vie des équipements
En adoptant une stratégie de maintenance préventive et conditionnelle, rendue possible par les fonctionnalités avancées d’un logiciel de gestion de maintenance, les industries peuvent prolonger la durée de vie de leurs équipements. Un entretien régulier et bien planifié réduit l’usure prématurée et les défaillances, ce qui permet de repousser les investissements en nouveaux équipements. Cette prolongation de la durée de vie des actifs industriels est un levier puissant pour la réduction des coûts à long terme.
L’implémentation d’un système de gestion de maintenance ne se limite pas seulement à la réduction des coûts immédiats. Elle apporte également une amélioration continue des processus de maintenance, offrant ainsi une vision claire et structurée de la performance globale de vos équipements.
En somme, l’optimisation des coûts de maintenance grâce à la GMAO équipements industriels n’est pas un simple argument de vente, mais une réalité concrète et mesurable pour les entreprises industrielles cherchant à améliorer leur rentabilité et leur efficacité opérationnelle.
Amélioration de la productivité et de la disponibilité des équipements industriels
L’intégration d’un système de gestion de maintenance dans vos opérations industrielles peut transformer la manière dont vos équipements fonctionnent au quotidien. En minimisant les interruptions non planifiées, un outil de gestion assure une augmentation significative de la productivité et de la disponibilité de vos machines.
Réduction des temps d’arrêt imprévus
Les arrêts non planifiés peuvent coûter cher à votre entreprise. Avec un logiciel de gestion de maintenance, vous pouvez suivre et analyser les performances de vos équipements en temps réel. Cela permet de détecter les signes avant-coureurs de défaillances potentielles et de planifier des interventions avant qu’un problème majeur ne survienne. Par exemple, une usine de production automobile a pu réduire ses temps d’arrêt de 25% en utilisant un système de maintenance pour surveiller les vibrations et les températures des machines critiques.
Optimisation des plannings de maintenance
Un système logiciel bien configuré permet de planifier les maintenances de manière optimale, en fonction des cycles de production et des périodes de moindre activité. Cela minimise les interruptions et assure que les équipements sont disponibles lorsque vous en avez le plus besoin. Prenons l’exemple d’une société de fabrication de produits chimiques qui a réussi à aligner ses opérations de maintenance préventive avec ses périodes de faible activité, augmentant ainsi sa disponibilité opérationnelle de 15%.
Amélioration des performances globales
En utilisant un outil de maintenance, il est possible d’identifier des opportunités pour améliorer les performances des équipements. Des analyses détaillées permettent de repérer des inefficacités et d’optimiser les processus. Par exemple, un fabricant de composants électroniques a pu améliorer l’efficacité énergétique de ses machines de 10% grâce à l’analyse des données fournies par son logiciel de gestion de maintenance.
Une solution logicielle de gestion de maintenance est donc essentielle pour maximiser la productivité et la disponibilité de vos équipements industriels. En réduisant les temps d’arrêt non planifiés, en optimisant les plannings de maintenance et en améliorant les performances globales, elle apporte une valeur ajoutée indéniable à vos opérations.
Gestion proactive et préventive des équipements industriels
La maintenance proactive et préventive joue un rôle crucial dans la gestion des équipements industriels. L’utilisation d’un système de gestion de maintenance assistée par ordinateur permet de mettre en place des stratégies efficaces pour anticiper les pannes et minimiser les interruptions de production.
Anticipation des pannes grâce à la maintenance préventive
L’un des principaux avantages d’un outil de gestion de maintenance est sa capacité à planifier des interventions régulières avant que les défaillances ne surviennent. En analysant les données historiques et en surveillant les indicateurs de performance des équipements, le logiciel peut suggérer des actions de maintenance à effectuer à des intervalles optimaux. Par exemple, dans une usine de fabrication automobile, le remplacement des pièces critiques peut être planifié en fonction des cycles de production et des heures de fonctionnement, réduisant ainsi le risque de pannes imprévues.
Optimisation des interventions de maintenance
Un système logiciel de gestion de maintenance permet également d’optimiser les interventions en fournissant des informations détaillées sur l’état de chaque équipement. Les techniciens peuvent ainsi intervenir de manière plus ciblée et efficace, en utilisant les ressources adéquates. Prenons l’exemple d’une centrale électrique : grâce à la solution logicielle, les équipes de maintenance peuvent accéder rapidement aux historiques de maintenance, aux manuels d’instructions et aux diagnostics en temps réel, ce qui facilite la prise de décision et la résolution rapide des problèmes.
Prolongation de la durée de vie des équipements
En mettant en œuvre une gestion proactive et préventive des équipements, les entreprises industrielles peuvent prolonger la durée de vie de leurs actifs. Un logiciel de gestion de maintenance permet de suivre l’usure et la dégradation des composants, et de prendre des mesures correctives avant que des dommages irréversibles ne se produisent. Par exemple, dans une raffinerie pétrochimique, la surveillance continue des pompes et des compresseurs permet de détecter les signes précurseurs de fatigue matérielle, permettant ainsi de planifier des réparations avant que des pannes coûteuses ne surviennent.
Réduction des coûts à long terme
L’adoption d’un système de maintenance proactif et préventif contribue également à la réduction des coûts à long terme. En évitant les pannes majeures et les arrêts de production non planifiés, les entreprises peuvent réaliser des économies substantielles. De plus, la gestion optimisée des stocks de pièces de rechange et des ressources humaines permet de minimiser les dépenses inutiles. Dans l’industrie agroalimentaire, par exemple, un logiciel de gestion de maintenance peut aider à maintenir un niveau optimal de stock de pièces détachées, évitant ainsi les surcoûts liés à des commandes urgentes et à des interruptions de production.
Un atout pour la conformité et la sécurité des machines
Assurer la conformité réglementaire
Dans le secteur industriel, la conformité aux normes et régulations est non seulement cruciale pour éviter des pénalités financières, mais aussi pour garantir la sécurité des opérations. Un système de gestion de maintenance aide à suivre et documenter toutes les interventions, assurant ainsi que vos équipements respectent les exigences légales et réglementaires. Par exemple, le logiciel peut générer des rapports détaillés sur les inspections et les réparations effectuées, facilitant ainsi les audits de conformité.
Amélioration de la sécurité des équipements industriels
La sécurité est une priorité dans les environnements industriels où les risques d’accidents peuvent avoir des conséquences graves. Une solution logicielle de gestion de maintenance permet de planifier et de suivre les interventions de manière rigoureuse, réduisant ainsi les risques de pannes imprévues et d’accidents. En surveillant en temps réel l’état des équipements, le système peut déclencher des alertes en cas de défaillance potentielle, permettant aux équipes de maintenance d’intervenir rapidement et efficacement.
Exemples concrets d’application
Prenons l’exemple d’une usine de production chimique. L’utilisation d’un outil de gestion de maintenance permet de suivre les dates d’expiration des certifications des équipements sous pression, garantissant ainsi que ces équipements sont inspectés et renouvelés dans les délais impartis. De même, dans une aciérie, le logiciel peut surveiller les niveaux de vibration des machines critiques et alerter les techniciens en cas de valeurs anormales, prévenant ainsi les pannes et les accidents potentiels.
Documentation et traçabilité
Une autre dimension importante est la traçabilité. Les systèmes logiciels de maintenance enregistrent toutes les actions effectuées sur les équipements, de la simple inspection à la réparation complexe. Cette documentation exhaustive est essentielle non seulement pour la conformité réglementaire, mais aussi pour analyser les tendances et optimiser les stratégies de maintenance. En cas d’incident, cette traçabilité permet de retracer les interventions passées et d’identifier rapidement les causes pour éviter leur récurrence.
En résumé, intégrer une solution de gestion de maintenance dans vos processus industriels n’est pas seulement une question d’efficacité opérationnelle, mais aussi de sécurité et de conformité. Les bénéfices sont multiples et tangibles, allant de la réduction des risques d’accidents à l’assurance de respecter les normes en vigueur.
Conclusion
Adopter une solution de gestion de maintenance assistée par ordinateur pour la maintenance des équipements industriels est un choix stratégique qui offre une multitude d’avantages. Que ce soit pour réduire les coûts opérationnels, améliorer la fiabilité des équipements, ou encore assurer la conformité réglementaire, la GMAO s’avère être un outil indispensable pour optimiser vos opérations industrielles. En centralisant les données, en facilitant la planification des interventions et en permettant une gestion proactive et préventive, elle renforce la performance globale de vos équipements.
Ne laissez pas les pannes imprévues et les inefficacités freiner votre productivité. Investissez dans une solution de GMAO pour transformer votre gestion de maintenance et atteindre de nouveaux niveaux d’efficacité et de rentabilité. En prenant cette décision, vous faites un pas important vers une gestion plus rigoureuse et performante de vos actifs industriels.
FAQ
1. Comment une GMAO peut-elle contribuer à la réduction des coûts de maintenance ?
Une solution de gestion de maintenance assistée par ordinateur permet de réduire les coûts de maintenance en optimisant les interventions et en prévenant les pannes. En surveillant en temps réel l’état des équipements, il devient possible de planifier des maintenances préventives plutôt que de réagir aux pannes, ce qui est souvent plus coûteux. De plus, la centralisation des données permet d’identifier les inefficacités et de rationaliser les ressources utilisées.
2. Quels sont les avantages d’une GMAO pour la fiabilité des équipements industriels ?
Une GMAO améliore la fiabilité des équipements en permettant une surveillance continue et une détection précoce des anomalies. Cela aide à prévenir les pannes imprévues, garantissant ainsi une meilleure disponibilité des machines. Par exemple, en suivant les indicateurs de performance tels que les vibrations et les températures, les techniciens peuvent intervenir avant qu’une défaillance majeure ne survienne, augmentant ainsi la fiabilité globale des équipements.
3. Comment une GMAO aide-t-elle à assurer la conformité aux normes et régulations ?
Un système de gestion de maintenance facilite la conformité aux normes et régulations en fournissant une traçabilité complète des interventions de maintenance. Les audits et inspections sont simplifiés grâce à l’accès rapide aux historiques de maintenance et aux enregistrements détaillés des interventions. Cela permet de garantir que toutes les actions effectuées sur les équipements respectent les exigences légales et réglementaires en vigueur.
4. Quelle est l’importance de la gestion centralisée des données dans une GMAO ?
La gestion centralisée des données est cruciale dans une GMAO car elle permet une analyse approfondie des performances des équipements et une prise de décision éclairée. En centralisant toutes les informations relatives à la maintenance, aux historiques des interventions et aux équipements, les responsables de maintenance peuvent facilement accéder aux données nécessaires pour optimiser les processus et améliorer l’efficacité opérationnelle. Cette centralisation facilite également la collaboration entre les différentes équipes de maintenance.
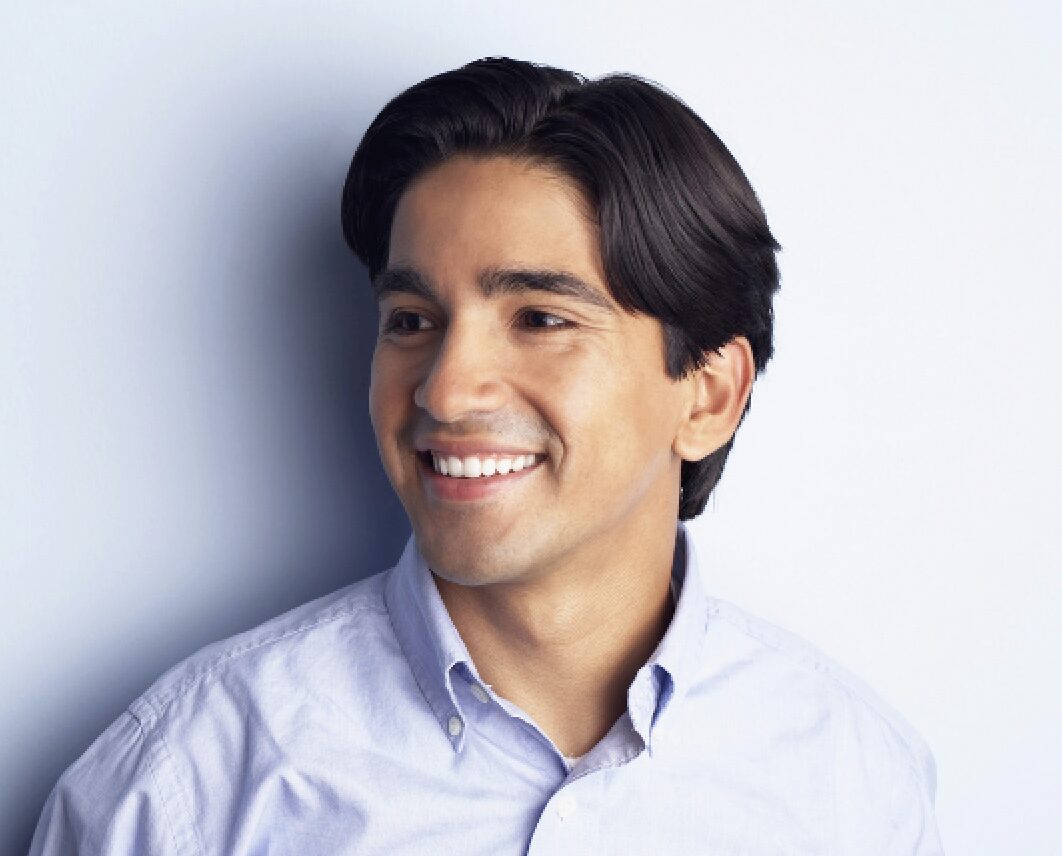
Consultant chez Solvay, j’accompagne les entreprises dans l’optimisation de leurs stratégies de maintenance, en mettant à profit mon expertise en GMAO et gestion des actifs industriels. Je partage également des conseils pratiques et études de cas sur gmao-industrie.fr, afin d’aider les entreprises à améliorer leurs performances opérationnelles.
0 commentaires